Safety
Laser safety in laser welding and laser cleaning
Laser welding safety deserves great attention. The welding process offers important advantages and can achieve a higher quality of the products in combination with more efficient production. As a guideline for safe laser welding, we should look at EN 60825-1:2014. This standard classifies lasers and sets requirements for the safety features associated with a specific laser class.
Laser welding machines and laser cleaning machines are class 4 lasers. In the classification of laser equipment, class 4 is the most hazardous category. Despite the risks, safe laser welding and laser cleaning are certainly possible.
Lasers with a power greater than 500 MW where humans have access to laser radiation fall under class 4. The powers used for manual laser welding and cleaning are often 1000 to 2000 watts. Lasers of this power can easily ignite materials or cause serious injury.
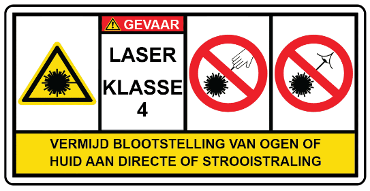
Features laser light
The laser light used in manual laser welding is in the non-visible infrared spectrum (IR-A). As a result, in addition to the direct laser beam, the reflections of the laser light are also not visible. The direct laser light and laser light that reflects specularly diverge to a limited extent, so the laser’s intensity can still be dangerous and harmful even at a great distance.
When aiming for a high degree of laser safety, it is, therefore, essential to also take into account (diffuse) reflections.
Risks of laser light
The laser light released during welding and cleaning harms the skin and eyes. Since the eyes do not detect non-visible infrared light, the eye will not close as it does with strong visible light.
Risks to the skin
Laser radiation can cause serious injuries to the skin. The severity of the course depends on the power of the laser beam. Another factor that determines how deep the laser burns into the skin is the wavelength. The wavelength of 1080 nm, used in most cases for manual laser welding and cleaning, gives deep penetration into the skin. The skin will heal after a burn but may leave scar tissue depending on the severity of the injury.
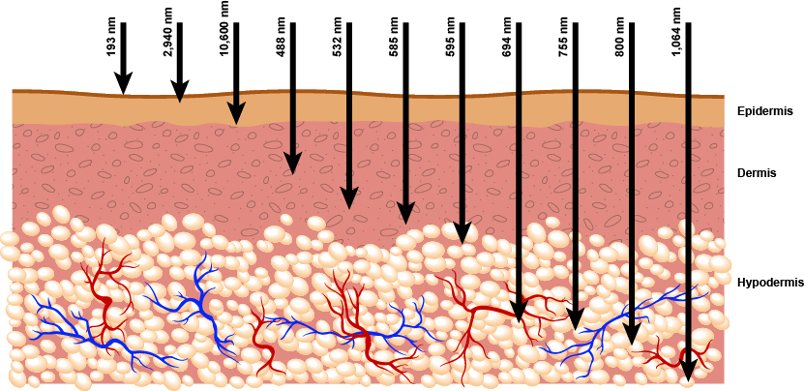
Risks to the eye
Depending on the wavelength, the eye will be damaged in other places by radiation with too high a power.
Wavelength 280-315nm
Radiation is absorbed in the cornea (Cornea)
Resulting in snow blindness welding eyes
Wavelength 315-400nm
Absorption of the light in the lens, the damage slowly builds up
Wavelength 400-1400 nm – visible light and infrared (IR-A)
Radiation is projected onto the retina (retina)
May cause burns resulting in blindness
Wavelength 1400 nm-1 mm – Infrared light (IR-B & IR-C)
The cornea absorbs most radiation
Resulting in retinal burns
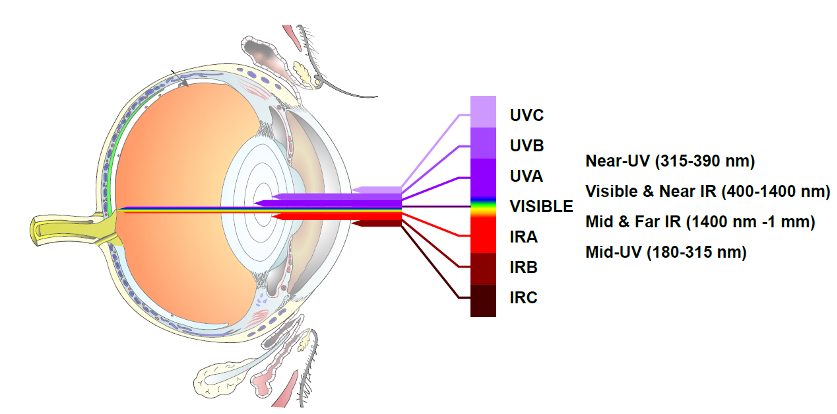
Occupational hygiene strategy
Following the occupational hygiene strategy is a good practice concerning limiting risks within companies when dealing with hazardous substances or processes. This method can also be used to create an environment in which laser welding can be done safely.
The following steps from the occupational hygiene strategy help to increase laser safety:
- Apply technical measures, work processes, equipment and materials that eliminate or limit risks.
- Take collective protective measures at source or take organizational measures.
- Provide personal protective equipment for employees who are or may be exposed to hazardous substances.
Practical laser safety steps
Safe laser equipment
Like all other machines, laser equipment must comply with several European standards and regulations, such as the Machinery Directive and the Low Voltage Directive.
EN 60825-1:2014 also applies to equipment incorporating laser technology. This standard describes the different types of lasers and the safety measures to be taken for a particular type of laser.
Requirements to be met for class 4 lasers:
- Fail safe control
- Key security
- Fail safe Interlock facility
- Warning stickers
- Fail-safe warning light
Shielding
Preferably, a laser welding installation should be used in an enclosed space. Such a space can be provided with an interlock circuit. Lighting can be installed on the outside to indicate the laser’s status (on/off).
This way, safe laser welding or cleaning can best be guaranteed. However, working with a fixed space is impossible in all cases.
This can usually be achieved with mobile shielding if you want to safely laser weld on location or in a large workshop. This shield must comply with EN 12254:2014-04. For selecting the right laser workplace shielding, the power and wavelength of the laser radiation must be considered. LAZRZ offers various products that can contribute to safe laser welding on location or in a workshop.
Laser safety training
Everyone who works with or in the vicinity of the laser must be well informed about the possibilities, operation, and risks of working with the laser. Safe laser welding or cleaning is not difficult if the employer and employees are well informed.
Personal protection
Personal protective equipment is indispensable when working safely with hand lasers. Much protective equipment cannot sufficiently withstand the direct (and long-term) laser radiation of a handheld laser welding machine or laser cleaner. However, the right protective equipment protects against short-term direct radiation or reflections. The right protective equipment makes working safely possible.
Laser safety goggles
The right type of safety glasses should be selected with due care. On the page regarding laser safety glasses, we further explain the right product selection.
Laser safety clothing and gloves
For selecting the right laser safety products, it is important that the welder’s clothing is matched to the type of laser. For many applications, the standards in the field of protective clothing are not yet sufficient. Protective clothing against laser radiation is available; leather welding clothing is also, in many cases, sufficiently protective against (short-term) laser radiation.