Benefits of handheld laser welding
Differences
Laser welding
TIG welding
Welding time
10 sec.
50 sec.
Accuracy
Minimal post-processing
Low distortion
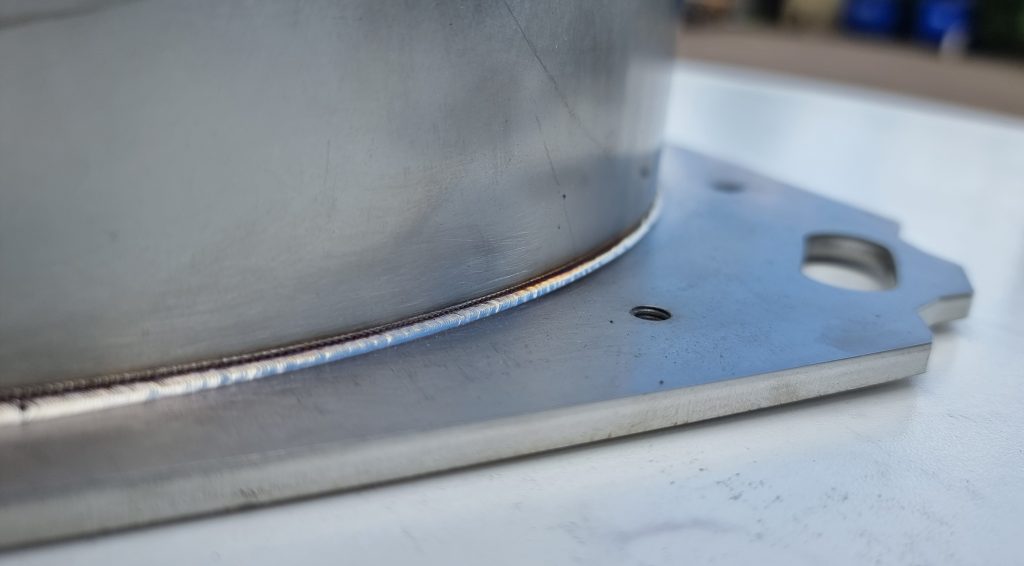
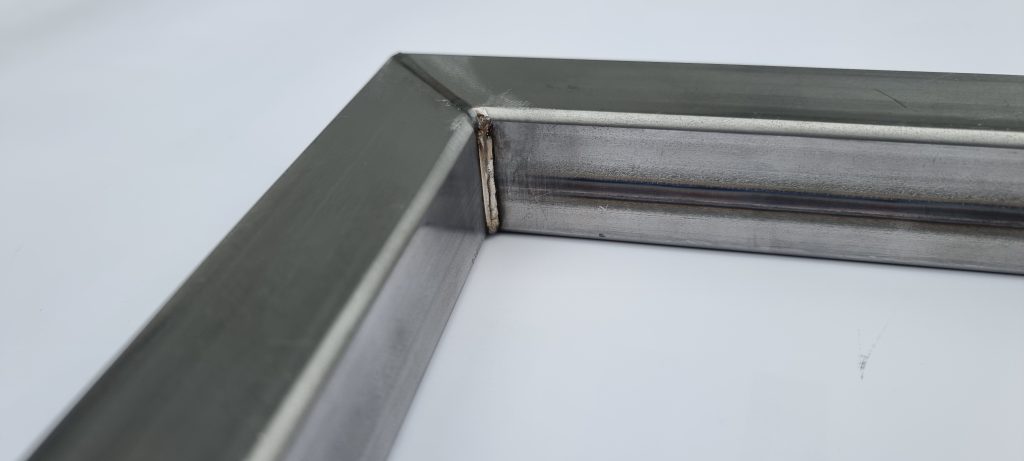
Benefits of handheld laser welding
- Fast
- Easy to perform
- Minimal post-processing
- Low heat input resulting in minimal material distortion
Manual laser welding is a welding process that can be used for a wide range of applications to achieve faster and better results. Especially in the processing of thin sheet metal, the high welding speed can lead to cost savings. The minimal distortion and attractive weld appearance help minimize post-processing costs as well.
Laser welding is fast
The travel speed in manual laser welding is significantly higher than in TIG welding. Laser welding can achieve a welding speed that is at least four to six times faster than TIG welding.
Laser welding is easy
The basic skills of manual laser welding can be learned within a few hours. The welder needs to develop a sense of the high speed and accurately position the laser spot. Welding I-joints is often easier when using a guide or stop. The welding gun can then be easily moved in the correct line.
Laser welding reduces post-processing
Due to the high speed and small molten pool, the area affected by heat is also small. The weld seam can be cleaned in almost all cases with a non-woven abrasive in one pass.
Laser welding minimizes distortion
Due to the very low heat input in laser welding, material distortion is often negligible. By using manual laser welding, time and effort required for clamping the product can be saved. Additionally, less time will be needed to straighten products after welding.